Facade Leasing
- 8
- 7 min to read
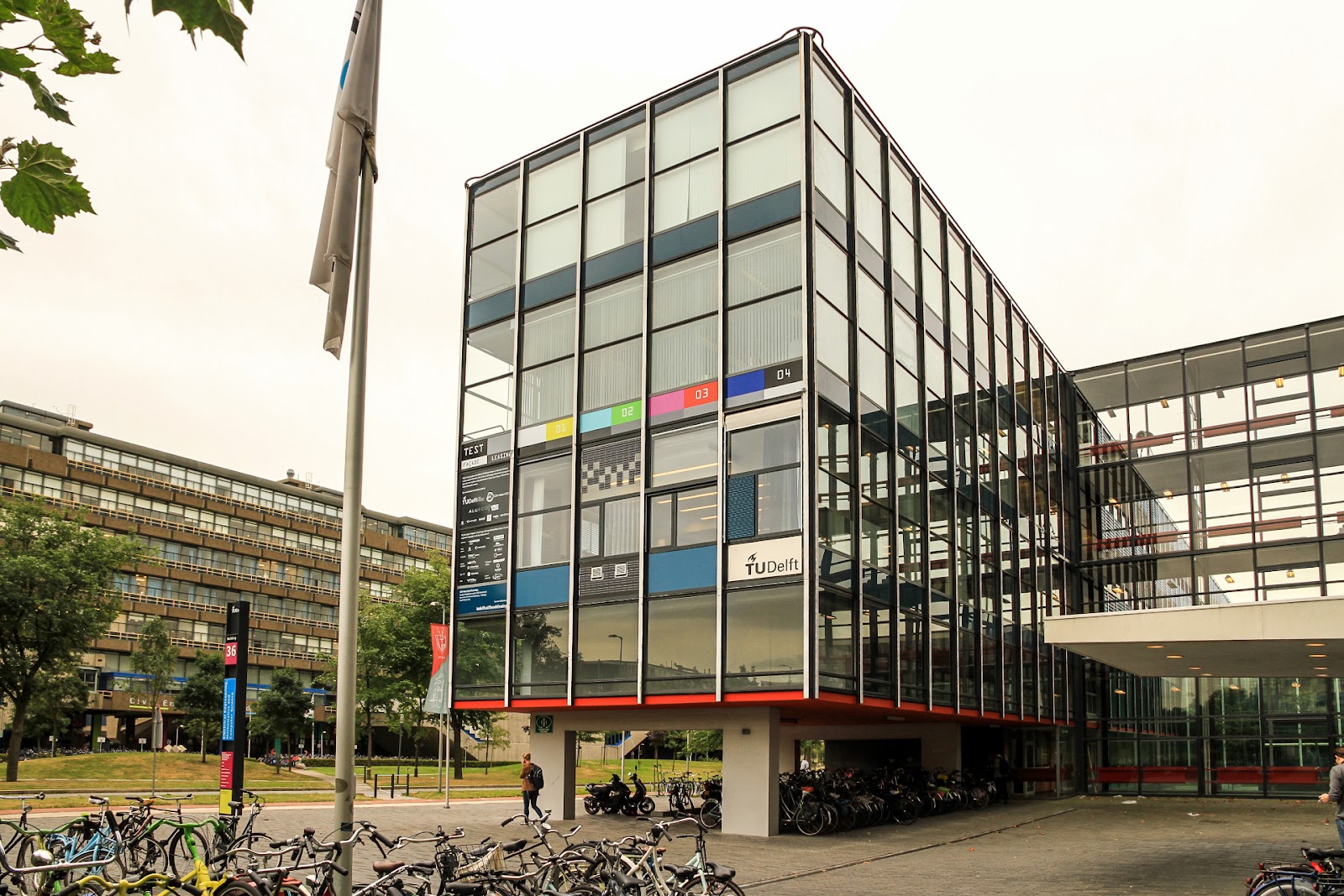
About the city. TU Delft applied to EIT Climate-KIC’s Pathfinder programme in 2015. Receiving an EIT Climate-KIC Pathfinder grant was critical in getting the project off the ground; it enabled the team to hire a dedicated researcher and to spend time working with the supply chain while generating interest in the proposals among the business community.
Goal
The project has two aims: first, to de-materialise this part of the construction industry by shifting the current business model to a product-service-systems, in which materials can be recovered and repurposed, reducing the environmental impact. Second, when façades are integrated into buildings with different technologies, they can vastly improve energy performance, making cost savings on energy consumption and reducing carbon emissions.
Implementation period. The first circular, multi-functional façade was installed in June 2016.
Fact
Across Europe, a large number of buildings constructed during the post-war boom of the 1950s to 1970s are quickly reaching the end of their original service life. Their façades and building systems are far below current standards, their energy consumption is unsustainably high, their spaces are in many cases uncomfortable and dysfunctional, and they are also very expensive to maintain.
Within the EU, buildings are responsible for 40% of energy consumption and 36% of CO2 emissions. Older buildings can be up to 20 times as inefficient in their energy usage as new ones
Solutions
Renovating buildings’ façades can improve energy performance and reduce energy demand, but current systems of production and consumption are based on a ‘take, make and dispose’ model, which uses energy and creates waste and pollution along the way. Conventional façades also tend to be part of larger, centralised control systems, which are often inefficient.
In September 2016 a consortium of companies, ranging from component suppliers to façade fabricators, installed a pilot project temporarily replacing a section of the façade on the low-rise building at TU Delft, EWI building. This enabled them to test technologies such as exterior sun-shading systems, ventilation and air-handling devices, LED media elements and automated operable windows.
Every new high-performance façade panel for this building is made of high-insulation aluminium framing and HR++ double-glazing and was delivered in a pre-assembled format, making it easy to install. Panels include automated sensors that drop-down solar screens during intense sunlight and high temperatures and pull the same screens up in wet and windy weather. Upper-level windows are automated to enable passive ventilation and night-cooling and a QR code on each panel keeps a history of maintenance schedules. These codes also collect data to allow the team to study the new façade’s impacts in terms of, for example, energy expenditure and indoor comfort.
This solution does not seek to address the particular problems of the EWI building’s future but instead uses the building’s representative quality as an icon of modernist architecture. Building such as the EWI, which are quickly reaching technical obsolescence, also display a degree of standardization and modularity that can make them the ideal target for deep energy retrofitting action, and hence for the implementation of new business model such as the one proposed by this project.
Challenges
Project financing for construction is typically secured by the market value of the property being financed, not by the provision of ongoing services.
To solve this problem, the team worked with Dutch bank ABN AMRO to produce an innovative financing mechanism where cash flows from façades work as bank guarantees
Team
TU Delft Faculty of Architecture and the Built Environment, Departments of Architectural Engineering + Technology and Management in the Built Environment
Timeline
In early 2018 the project consortium has received further funding for the upscaling of this research pilot project to a large scale practical demonstrator case-study.
Primary energy use has fallen by around 75%, from 189 kWh/m2 to 48 kWh/m2, saving between €35,000 and €40,000 a year.
If you notice an error or inaccuracy in our editorials, please email [email protected] so we can look into it.